More About Alcast Company
More About Alcast Company
Blog Article
3 Simple Techniques For Alcast Company
Table of ContentsThe Facts About Alcast Company RevealedThe Only Guide for Alcast CompanyThe smart Trick of Alcast Company That Nobody is DiscussingThe 3-Minute Rule for Alcast CompanyThe 5-Second Trick For Alcast CompanyA Biased View of Alcast Company
The refined difference depends on the chemical web content. Chemical Comparison of Cast Aluminum Alloys Silicon promotes castability by lowering the alloy's melting temperature and improving fluidity during casting. It plays a critical role in enabling intricate mold and mildews to be filled accurately. Additionally, silicon adds to the alloy's stamina and use resistance, making it useful in applications where durability is critical, such as automotive components and engine parts.It also boosts the machinability of the alloy, making it much easier to process right into completed products. In this way, iron adds to the overall workability of light weight aluminum alloys.
Manganese contributes to the toughness of aluminum alloys and boosts workability (Casting Foundry). It is frequently made use of in functioned light weight aluminum items like sheets, extrusions, and profiles. The visibility of manganese aids in the alloy's formability and resistance to breaking throughout fabrication procedures. Magnesium is a lightweight aspect that offers toughness and impact resistance to light weight aluminum alloys.
A Biased View of Alcast Company
Zinc boosts the castability of light weight aluminum alloys and aids regulate the solidification procedure throughout spreading. It boosts the alloy's toughness and hardness.
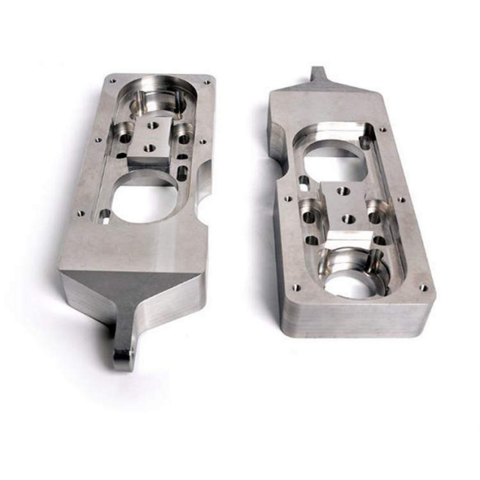
The primary thermal conductivity, tensile toughness, return stamina, and elongation differ. Amongst the above alloys, A356 has the greatest thermal conductivity, and A380 and ADC12 have the least expensive.
Alcast Company - An Overview
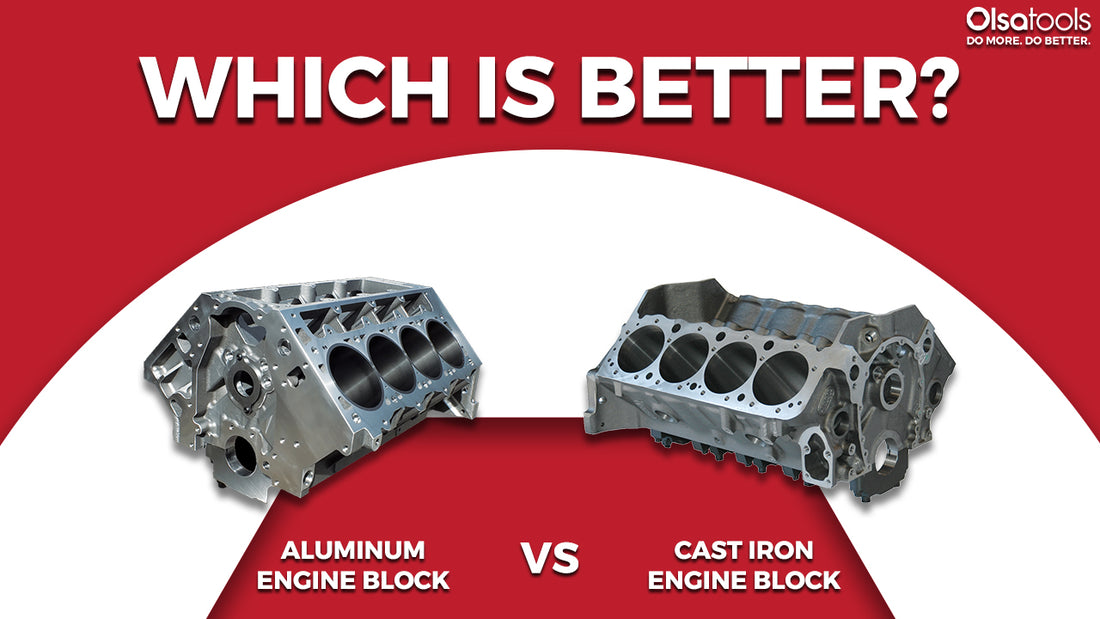
In accuracy casting, 6063 is appropriate for applications where complex geometries and top quality surface finishes are vital. Instances include telecommunication enclosures, where the alloy's exceptional formability enables for smooth and visually pleasing designs while maintaining architectural honesty. In the Illumination Solutions industry, precision-cast 6063 parts develop sophisticated and efficient lights components that require intricate forms and excellent thermal performance.
It brings about a finer surface area coating and much better corrosion resistance in A360. Moreover, the A360 shows premium elongation, making it suitable for facility and thin-walled elements. In precision spreading applications, A360 is well-suited for industries such as Customer Electronics, Telecommunication, and Power Devices. Its enhanced fluidness allows for detailed, high-precision components like smartphone cases and communication tool real estates.
Alcast Company Things To Know Before You Get This
Its unique properties make A360 a beneficial option for precision casting in these sectors, improving product resilience and high quality. Aluminum Casting. Light weight aluminum alloy 380, or A380, is a commonly used spreading alloy with a number of distinctive features.
In precision casting, light weight aluminum 413 shines in the Consumer Electronic Devices and Power Equipment industries. This alloy's exceptional deterioration resistance makes it an exceptional selection for outdoor applications, making sure long-lasting, long lasting items in the mentioned industries.
A Biased View of Alcast Company
Once you have determined that the aluminum pass away casting procedure is suitable for your job, a crucial next action is picking the most suitable alloy. The aluminum alloy you pick will substantially impact both the spreading process and the homes of the end product. As a result of this, you should make your decision thoroughly and take an informed strategy.
Establishing the most appropriate light weight aluminum alloy for your application will certainly mean considering a vast range of features. The first group addresses alloy features that impact the manufacturing procedure.
The 15-Second Trick For Alcast Company
The alloy you select for die spreading directly impacts a number of aspects of the spreading procedure, like just how very easy the alloy is to deal with and if it is prone to casting flaws. Warm splitting, likewise known as solidification splitting, is a normal die spreading issue for aluminum alloys that can cause internal or surface-level tears or splits.
Certain aluminum alloys are more at risk to warm breaking than others, and your selection needs to consider this. One more usual problem discovered in the die casting of light weight aluminum is die soldering, which is when the cast sticks to the die walls and makes ejection hard. It can damage both the actors and the die, so you need to try to find alloys with high anti-soldering properties.
Rust resistance, which is currently a significant quality of aluminum, can vary considerably from alloy to alloy and is an important characteristic to consider depending upon the environmental conditions your product will be exposed to (Foundry). Put on resistance is an additional residential property generally sought in light weight aluminum products and can distinguish some alloys
Report this page